There are three reasons the manufacturing industry is moving quality control to the cloud: to standardize, adapt, and empower the quality improvement team.
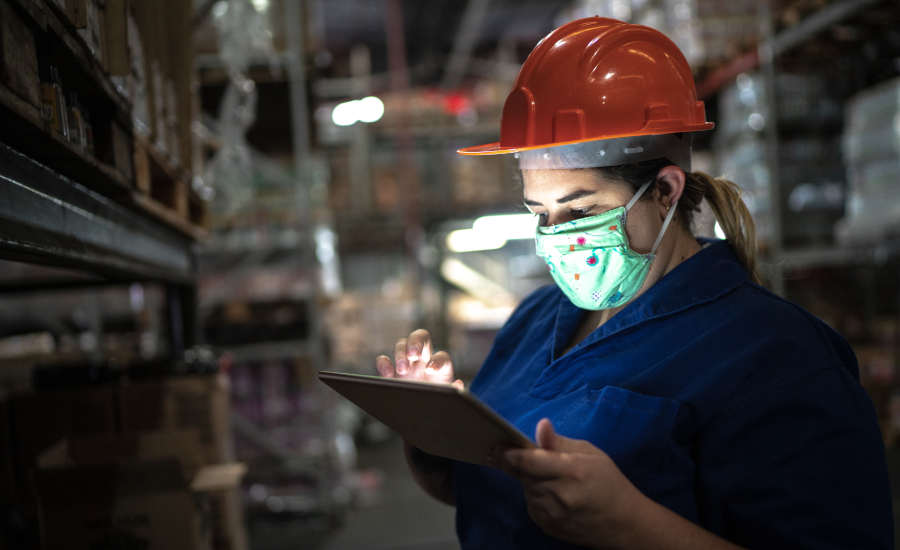
Everybody’s writing about it. “Move to the cloud now!” “Don’t wait!” “Buy now!” It’s a hot topic, and rightly so. Cloud-based quality software provides three indispensable requirements for manufacturers today: centralization, flexibility, and power. These three capabilities bring statistical process control (SPC) to your manufacturing quality endeavors in ways that are gamechangers for many organizations.
These capabilities also comprise the heart of InfinityQS quality software products. With a cloud deployment, you can easily and rapidly reap significant benefits.
Centralization
Let’s put this as succinctly as we can. Centralizing your quality data buys you standardization, visibility into that data, and the potential for a real transformation of your operations.
Centralizing your quality data is the key. Here’s why.
Centralizing your quality data is the easiest way to standardize. Standardizing naming conventions (e.g., product codes, feature names, lot number formats) is crucial. Not only does it ensure a common code of communication across all plants, but it supports system-to-system integration and enables simplified high-level reporting and data analysis across all plants.
In addition, it limits the confusion that is so common in organizations today when individual plants invent their own systems, naming conventions, and standard operating procedures (SOPs).
For example, when you standardize naming conventions, your quality management system can easily aggregate data across production lines and plants without complex database queries. You can access corporate-wide quality insights that are generally impossible to uncover without standardization. Aggregating your quality data provides you with the visibility—a bird’s eye view—you need to transform your operations.
So, let’s say you standardize naming conventions and wisely store all quality data in a single, centralized repository (as we do with InfinityQS cloud-based quality software products). Your quality experts can then review and analyze that data weekly or monthly—comparing quality performance across lines, products, or shifts—and come up with a list of quality issues for your Six Sigma experts to attack.
If so, you’re well on your way to incorporating the most effective continuous quality improvement activities in your operations—and that’s what keeps your products moving out the door, your customers happy, and your bottom line in the black.
Many companies want to calculate and compare process capability to see which processes are performing well and which ones need help; this gives managers the info they need to focus their resources on the top issues affecting performance.
In essence, what you’re looking to do with the big picture is extract manufacturing intelligence. You just need a system that supports plant floor, enterprise-wide data collection, and a means of aggregating that data so you can make it easily consumable and understandable by managers, engineers, and quality professionals.
Flexibility Means A Lot
Flexibility is something every organization strives for, in one way or another. It is the “agility” we all seek these days. It means having the ability to turn on a dime. When demand is up, you’re ready for it and ramp up production accordingly. When demand is down, you cut back a bit and keep your operations going while still making your numbers.
Flexibility in quality management software means a whole lot more. When you think of your workforce, it means cross-pollination. When an operator is down, it’s nice to have someone step in and take over. When healthcare concerns push your staff into remote work (sound familiar?), it’s great to have a system that supplies the critical data your people need to collaborate and work efficiently.
And when you make the move to the cloud, it’s comforting to have a system that is easy to deploy and learn how to use. That’s a lot of flexibility.
Flexibility is important in pursuing your overall quality goals because each company is different — different equipment, different data collection strategies and solutions, and different issues.
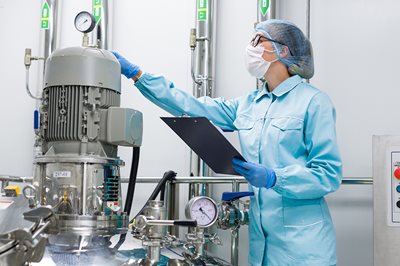
Cross-Pollination
Over the years, manufacturing employees attain tribal knowledge. Operators know the personalities of their machinery. Plant floor supervisors have almost a sixth sense about how to run their production operations. That knowledge is locked in the heads of those experienced people. If your workers can’t be on the plant floor, then you’re losing your company’s tribal knowledge—or it’s seriously eroded.
With a cloud-based quality system, you can transform that tribal knowledge into digital foundations. In cloud-based quality systems, you can capture and convert that tacit tribal knowledge into explicit rules, procedures, processes, and workflows and ensure that they are consistently implemented.
This enables you to drop Operator A into Operator B’s production line when the need arises and not lose a beat. That’s cross-pollination. It’s keeping your lines running when staffing is a challenge.
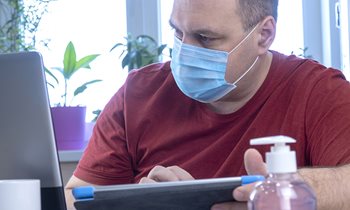
Going Remote
Going remote means more than just working from home. It means being remote from the plant floor. Most manufacturers are restricting the number of personnel who can be on the shop floor at any given time. They separate the floor into sectors, then limit who can enter each sector. So, that might mean that a production supervisor has to do her job from an office on site, but not actually walk the floor.
Remote working is becoming a permanent reality. InfinityQS quality management software enables you to move your manufacturing efforts into the new era. The best way to achieve a remote workforce while maintaining unification and centralization of all your data is in the cloud via Software-as-a-Service (SaaS) solutions.
Your quality management practice is a great place to start your digital transformation journey. The cloud facilitates an impactful system that is affordable and easy to implement, unlike more complex plant information systems. And, when you are ready, our quality systems can integrate with other plant software systems.
Easy Deployment and Sustainability
Deploying to multiple sites with an on-premises quality system means more hardware, more licenses, and more infrastructure. Cloud-based systems eliminate that overhead. You just buy subscriptions, give users the password, and they’re in the system! Deployment could not be any easier.
Learning to use an InfinityQS cloud-based quality management system is also a snap. Our software products are perfectly suited to remote learning. E-learning modules, available in a robust, context-sensitive system, are currently available in English, German, and Spanish. Instructions, tips, videos, tutorials, best practices, getting started guides, FAQs, industry examples, and more are just a click away for users.
We updated the Support section of our website to offer ways to help you build your knowledge and expertise in our products. We’ve got tons of information for administrators and super users—information you need to administer and manage your InfinityQS software deployment. It never hurts to have as much in-house expertise as possible so you can get the most value from your InfinityQS software.
Our Support section will help you save time and effort as you work to get everyone up to speed, solve issues, and get your questions answered.
Finally, perhaps one of the most flexible things that a cloud-native system can do for you is updates. Not upgrades—but updates. There are no servers to purchase and setup, no software to install, and no need for time-consuming software upgrades. Your staff will always have the latest and greatest software version on any device with a browser.
The Power of the Cloud
The power of the cloud is many things to many organizations. For manufacturers, it’s delivering real-time data to people who can use it most effectively to minimize production issues, head off potential problems, and find best-case scenarios for utilizing your precious resources.
Cloud applications provide the most information and capability while using the least IT resources. They are incredibly efficient for companies. You get more for your money because cloud technology helps reduce costs.
Software-as-a-Service (SaaS) quality management systems are breaking the long-standing paradigm of how quality is managed in manufacturing.
That’s the power of the cloud in action. It helps you standardize quality improvement efforts, adapt quickly to changes in the plant or production line, and empower your Six Sigma team to do what they do best — identify the greatest areas of need for quality improvement and implement changes.
We invite you to explore our cloud-based quality intelligence solutions, ProFicient and Enact, to discover more about the values of moving to the cloud. If you’re ready to start transitioning now, learn how you can try Enact free for 3 months.